This post is mostly for my own reference, and also to replace and supplement information that used to be hosted at http://soundofmusic.se/ but is no longer available.
My Roland A-80 keyboard has a pretty noisy action, and after the success I had replacing the key felt strips in the Korg M1, I figured I should give the A-80 the same love and care.
According to Gearslutz, the A-80 features a Matsushita SK-688 keybed – it’s an older keybed (but it checks out) – and Syntaur have some replacement parts available, including a felt strip suitable for the keybed “lowers”, where the keys rest when they are not being played. I ordered two units, on a hunch (turns out I was right).
When they arrived, it was time to begin the service operation.
Before you begin
I highly recommend getting a copy of the service manual. I’ve saved you the bother of finding it: here it is. That’s the PDF I use, hosted on our site. (It’s not perfect but it is the best resolution and clearest copy I could find online.) I kept the PDF open on my desktop, and flipped between pages as I worked.
Secondly, you will need a key removal tool. There are instructions in the manual on Page 5 on how to make one using a paper clip, and providing you are able to match the dimensions specified, it actually works.
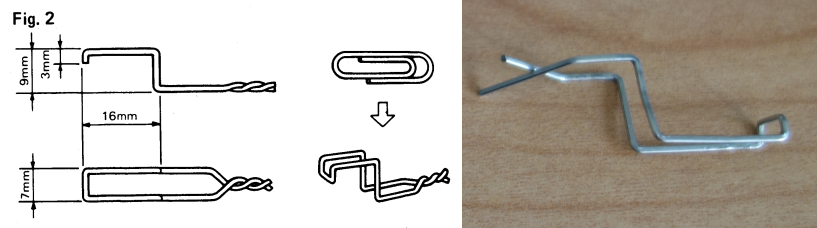
However, it is awkward to use, and not too robust for intensive use. (I went the extra mile and sacrificed a teaspoon for the cause. More on that later. If you don’t have access to a basic workshop, be assured that the paper clip tool does work.)
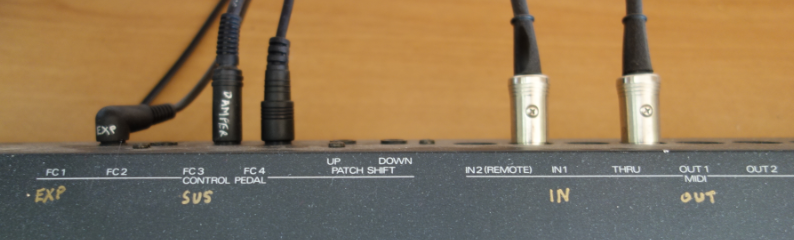
Wherever you move the unit to, make sure it is at a comfortable working height. I initially placed it on a “standing desk” but this was really too high. I should have just used a regular-height table. The A-80 weighs a ton. (30 kg?). Most of that weight is concentrated at the front edge (each key is weighted at the tip and that is where most of the weight comes from).
Opening the Lid
The top is hinged at the back edge and flips up like a car bonnet, once you have removed some screws from the bottom of the unit. Page two in the Service Manual has the details but I’ve got a diagram from another post about the A-80 which I’ll re-use here:

You either need to flip the unit on its back, balance it upright on the back edge as you remove the screws. Either way, it’s awkward and risky. (It was at this point I realized the standing desk was probably a bad idea.) Restoring it to the normal position, the lid then swings up for easy access.
If I recall correctly, there’s an earthing wire that will possibly prevent the lid opening to a useful working angle. In my unit, I’ve lengthened the wire so that I don’t have to unscrew one of the lugs, but your unit may be different. Use caution.
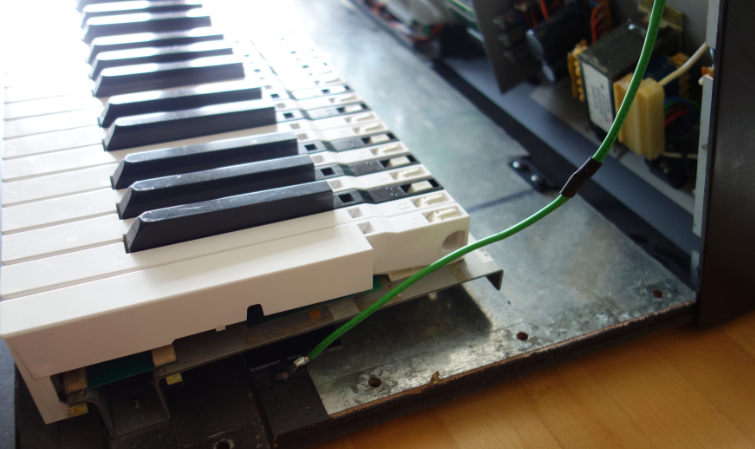
Now we’re ready for the next step.
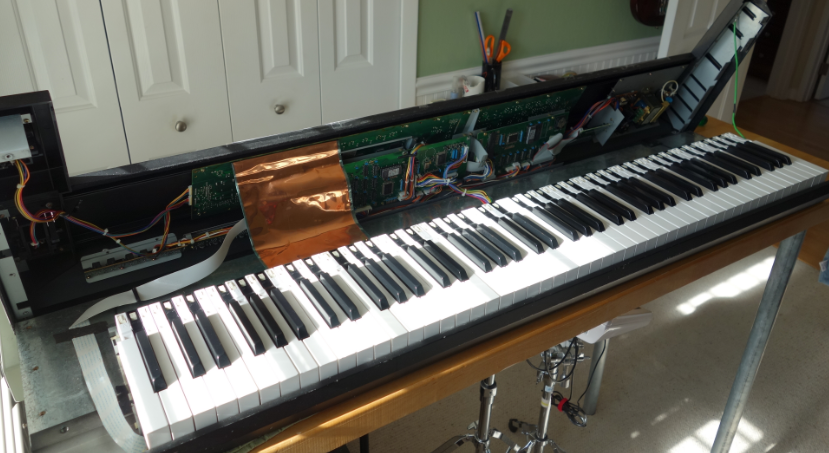
Removing the keybed
If you’re only interested in removing the black keys, you don’t need to remove the keybed from the chassis: Black keys slide out towards the back; White keys towards the front (where there is no room in the assembled unit.
Removing the keybed requires:
- Disconnecting the cables;
- Unscrewing the keybed from the base.
Disconnect the copper shield
It’s attached to the keybed by three screws:
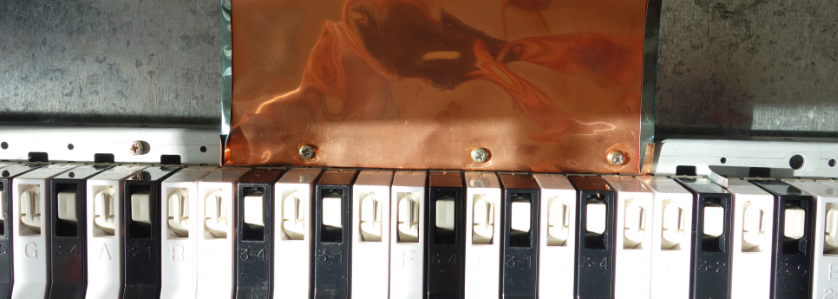
Unplug the “key pressure” ribbon cable
It is easy to unplug the cable from the CN8 connector on the MAIN-A board:
Mark the ribbon with a sharpie so you can re-connect it correctly later (optional). The receptacle clamps down on the ribbon edge and easily releases the cable if you tug gently on the grey section of the connector to open it:
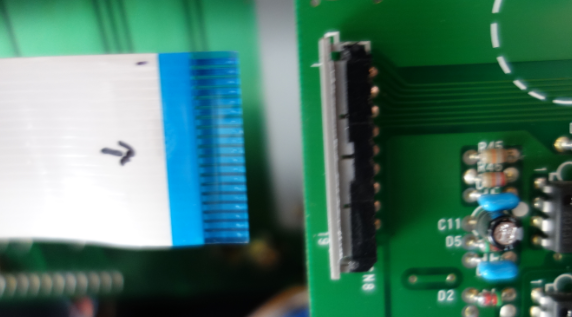
The ribbon cable is retained by a flexible clamp, and in my unit, a strip of tape holding it to the base plate.
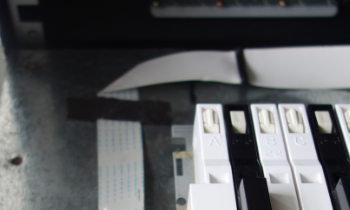
Unplug the PCB connectors RA1, RA2, RA3
In my unit I had to snip a cable tie that was grouping all the wires together. Now that I write this, I realize that I forgot to replace it. Oh well, no big deal. RA1, RA2, and RA3 are marked on the PCB.
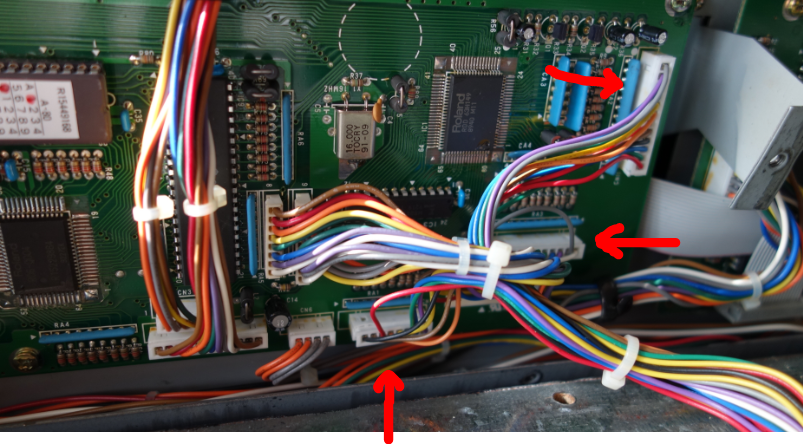
If necessary, you can use a small screwdriver to loosen the connectors. They are keyed, you can only insert them one way.
Unscrewing the keybed from the chassis
There are 12 screws to remove: 6 from the inside back edge, and 6 from the underside at the front of the chassis. These are indicated as “II” and “III” in Fig.1 above.
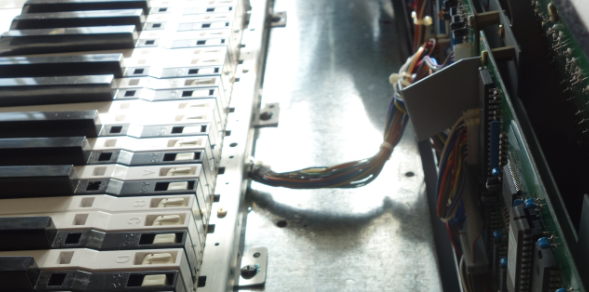
Now we can lift the keybed out of the chassis and place it on a clean padded work surface. Take care to protect the ribbon cable – it is still attached, and is fragile.
Now would be a good time to take a vacuum cleaner to the interior of the chassis. I don’t know about you, but my unit was pretty filthy inside under the keys.
Reviewing the keybed
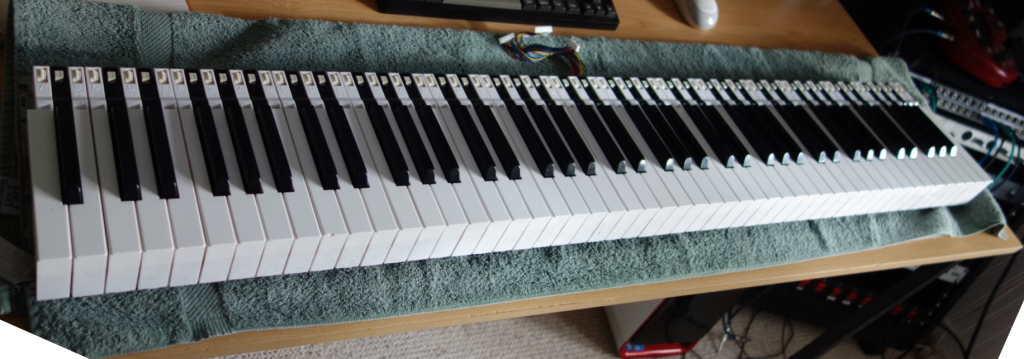
Replacing the felt “lowers” means that I’m going to have to remove all the keys. I took some time to review the keys. Each key has an identifier embossed near the hinge. For White keys, its the Scale note (except for one B key which also says “2-2”, and the first and last keys which are A’ and C’ respectively). The Black keys seem to be a random 3-1, 3-2, 3-3, etc, up to 3-6. I can’t see a correspondence between scale position and number.
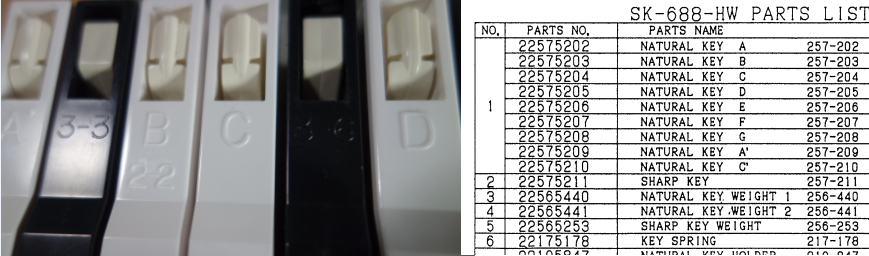
The parts list on page 4 of the service manual does not give any hints about these codes. I don’t think it is significant, apart from the obvious non-standard keys at the top and bottom ends of the keybed. However, as I put the removed keys aside, I made sure to line them up in order so that I could replace them exactly the same way. I recommend that you do the same.
Removing the keys
Each key consists of a key Holder that is attached to the base, and the Key itself which hinges on the holder, and depresses when you play a note. Removing a key from the base involves reaching through a hole in the Key and lifting a catch on the Holder to allow the holder to be slid out of the base. White keys slide towards the front, whilst Black keys slide out towards the back.
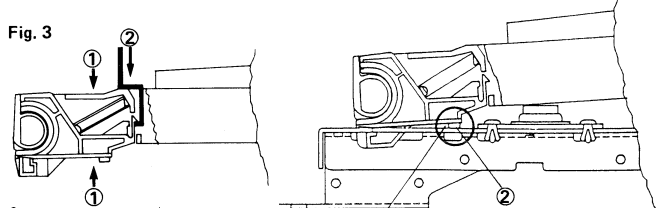
Page 6 of the Service Manual attempts to describe the process clearly, but in all copies I’ve found on the Internet, there appears to be some text missing.
Essentially, the process is:
- Depress the Key
- Insert the key removal lever and rock it towards you so that the tooth engages the Key Holder latch (it is exposed while the Key is depressed)
- Lift the key removal lever slightly to ensure the lock button at the base of the Key Holder is raised out of the hole in the base
- For White keys, push at the back to slide the Key Holder towards the front.
- For Black keys, push on the front of the key to slide the Key Holder towards the back of the base.
- The Key + Key Holder should then lift away from the base.
Having a look at base with keys removed make this more understandable:
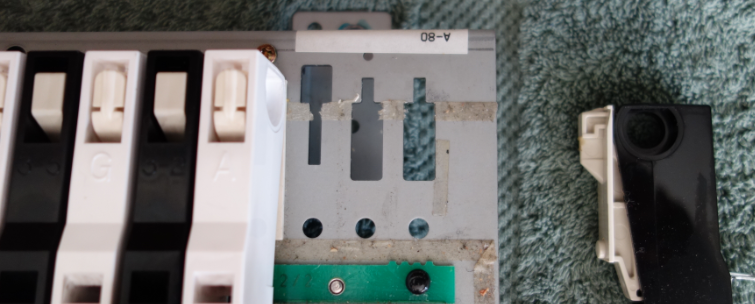
The Key Holders fit into the notches in the base plate. Black keys lock in from the back; White keys lock in from the front. You can see the round hole that the lock button fits into… here’s a view from the back:
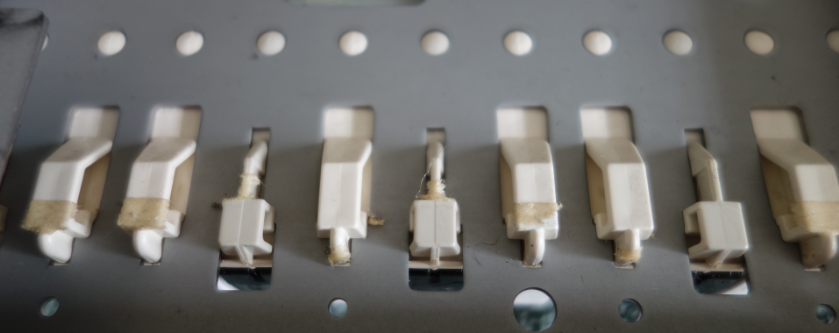
The key removal tool is for lifting that button out of the hole, via the tooth latch on the key holder.
There’s nothing like trying it out in practice.
One thing you may encounter is that there is a whole lot of double-sided sticky tape all over the base plate, and the key holders are very firmly held in place. It took some force to dislodge them. Sliding them out while holding the key removal lever in place was tricky.
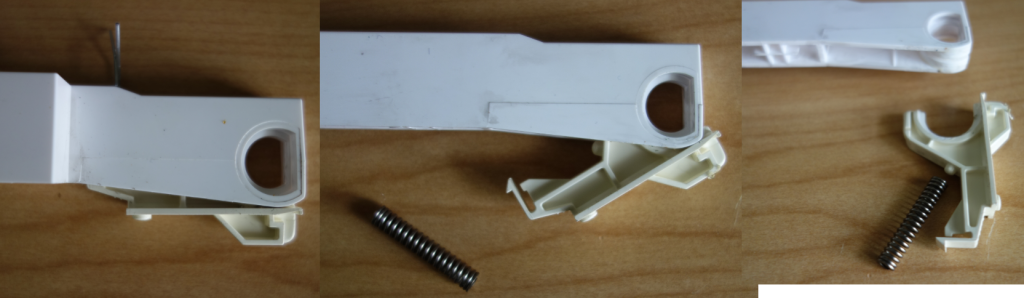
When I started removing the keys, the holder and key would separate and the spring would fall out. Not a big deal to re-assemble, but it’s best to avoid it if possible. Knowing the mechanics ahead of time might help with this.
With the paper-clip version of the Key Removal Tool, I had difficulty lifting the Key Holder lock. Seeing as I was starting from one end and removing all keys, I could use a small screwdriver from the open side to assist in the release:
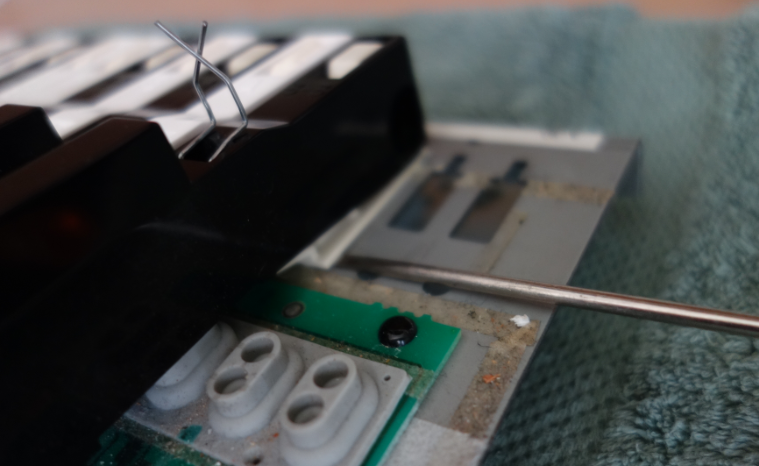
However, using a screwdriver has risks. After two decades or so, those rubber domes are fragile. USE CAUTION! DO NOT LET THIS HAPPEN:
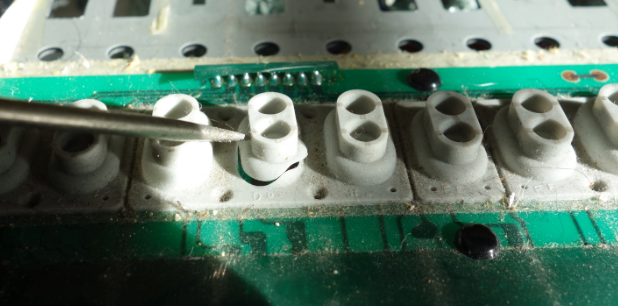
That’s the D4 key. So long as I don’t poke it, I can’t see the break in the rubber, and I had to hope that the switch was still functional. If not, I’d find out later.
Things were much easier when I gave up on the paperclip and manufactured my own key removal tool.
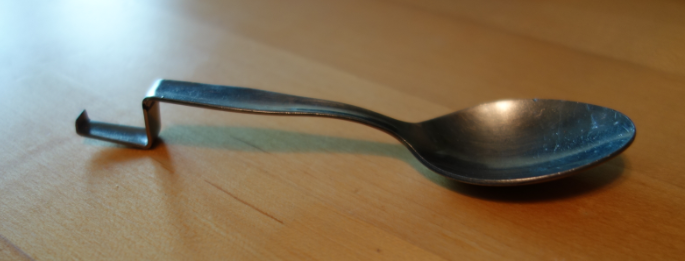
The thickness of the “blade” at the business end isn’t specified, but the thinner and more polished it is, the easier it will be able to latch on to the plastic catch inside the key.
Imagine you needed a knife for something, couldn’t find one cause all you found was 10 000 spoons…. it could happen!!! And therefore you couldn’t do whatever it was you needed the knife for, and then the next day it turned out that a spoon would have done.
Ed Byrne
With all the keys removed I debated trying to remove all the old excess double-sided tape, and decided that, maybe it was there for a reason, and left it.
Replacing the key felt
This part was easy. It’s also the part where I realized that it was a good thing I ordered two units of key felt, because it took one unit just for the White keys alone.
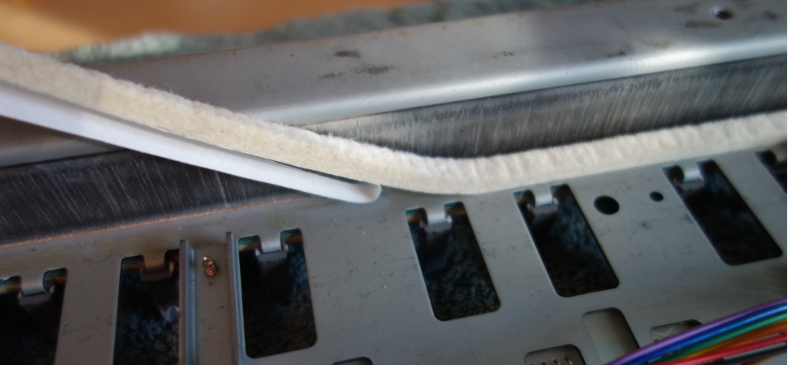
This new felt feels a little thicker than the old strip.
With the felt replaced, we can re-insert the keys. No special tool is required for this.
Be warned that the thicker layer of felt on the underside means that there is slightly less room available when maneuvering the key into place. I took my time and tried to protect the rubber domes as much as possible from accidental shear forces as the key holder slid into the slot and locked in place.
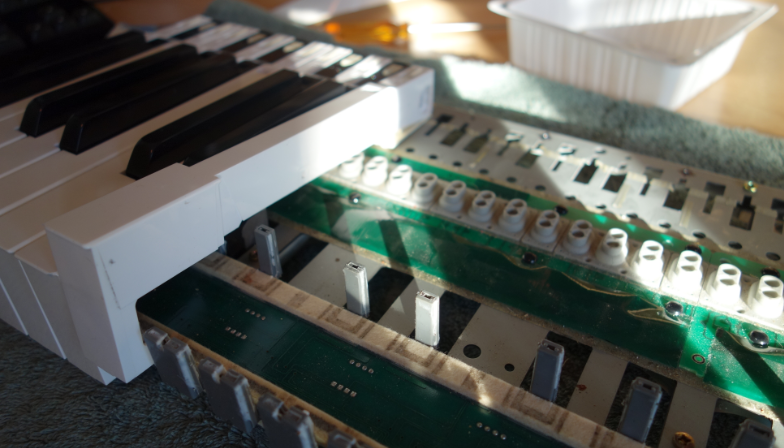
Problem #1
A side goal of this whole adventure was to take a close look at C#5 which has always been a little “sticky”. It never quite bounced back as quickly as it should, and very occasionally stuck in the depressed state. Sure enough, when I re-inserted it into the base, the same behavior – actually worse – was observed.
Process of diagnosis:
- I tried swapping the grey plastic guide with one from a known “good” black key position, and observed the same problem.
- I swapped the key itself with a “good” one and, again, observed the sticky bounce-back.
- I removed the guide completely, and the key bounced back freely – nice – but with a lot of unacceptable “slop” from side to side.
I decided that either the guide post itself must be bent (not visually apparent), or the key holder slot slightly out of alignment (I find that hard to believe).
The solution I settled on involved removing the grey plastic guide and shaving the sides down a fraction, then re-lubing with a slight amount of grease. Fortunately this was sufficient and the re-installed C#5 key now returned to the upright position snappily. Success!
Reconnecting and Testing
With the keys restored to position, I lifted the keybed back into the chassis and screwed it in place; Reconnected the plugs and ribbon cable, and copper shield.
Anticipate the worst
- You’re going to need to connect the mains power and a MIDI out cable;
- You’re going to need to test every key on the board, with a sound source that is responsive to velocity;
- You’re going to find out that something isn’t working;
- You’re going to have to go back in to the keybed and try to fix it.
Alternatively, just screw the lid back on and heft the A-80 back into your normal position in the studio, and hope for the best. I chose this second option. I recommend that you suppress your optimism, and assume the worst. Get the A-80 into a place where you can test the MIDI output and still investigate keybed issues.
First good news: I found that the D4 functioned normally. That damaged rubber dome switch isn’t affecting the key response. Phew!
Problem # 2
However, G#4 seemed WAY too sensitive, belting out a velocity close to 127 no matter how gently I pressed the key. Ugh.
There’s nothing for it, but to open the lid and remove that key and examine the rubber dome switch.
Pro Tip: If you are diagnosing a Black key, then you do not need to unscrew and move the keybed from the chassis.
I unscrewed those 12 screws, and moved the keybed back towards the rear of the chassis to get clearance at the front; then raised it up an inch or so on wooden blocks so as to give all keys a clear travel path when depressed.
Then I realized that I didn’t need to do any of that, because I was only interested in one Black key. And they pop out from the back of the keybed, not the front.
After removing the key, I pressed the rubber dome with my finger. It seems that it was possible to emit notes with a wide range of velocity values. The dome switch did not appear to be at fault, but it is hard to judge sensitivity with a finger.
I tried carefully re-installing the key, to see if it was just debris or dust, but it didn’t make a difference. I also tried swapping over to a different Black key to see if it helped. It made a slight difference but still not acceptable – it was just too hard to get softer notes and compromising playing technique for that one key is not really feasible.
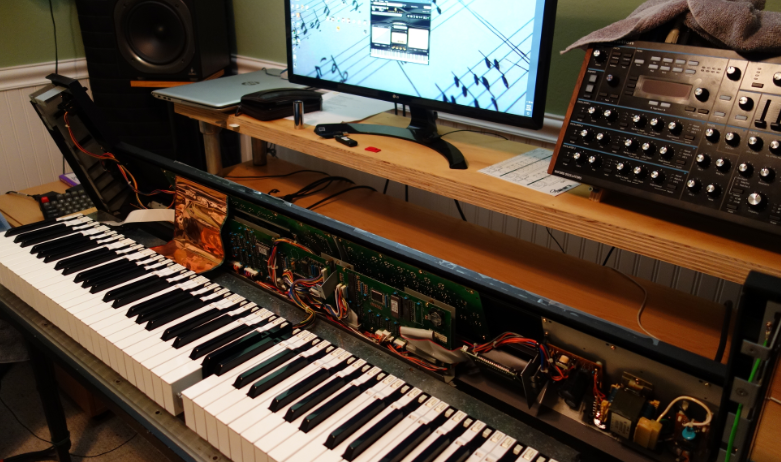
I examined the black plastic key at the point where it pushes down on the rubber dome switch. You can see from the schematic further back in this post (Fig.3) how the key, when depressed, impacts the dome switch at an angle. This causes the switch to close two sets of contacts in quick succession, and the time difference between the two circuits closing is translated to “key velocity”. It’s pretty accurate, when working correctly.
For whatever reason, this specific rubber dome was closing the two switches almost instantly, regardless of actual key depression rate.
In desperation, I took a file to the key and very carefully induced an angle in the flat underside of the key, such as to accentuate the timing difference in how the key impacted the two parts of the rubber dome. I don’t have a photo of this unfortunately (I wish I did, but I’m not opening up the A-80 again to get one).
Installing the key and re-testing demonstrated that my hack had made a difference. The velocity response on G#4 was now closer to that of the other keys. It’s not perfect but it’s very usable. It is still a “sensitive” key. I can live with it.
Conclusions
On the whole, the operation was a success. I think I dodged a bullet with the torn rubber dome on D4, and taking a flat bastard file to a key component to fix the problem on G#4 isn’t ideal by any means, but it seems to have worked. C#5 is no longer sticky.
The keybed is about 50% quieter and feels smoother. I did not replaced the “down” felt because it is aligned with the polyphonic after pressure sensors and I wanted to avoid messing with those. But much of the noise was due to “bounce-back”, and that has been reduced a lot.
The Black keys seem unaffected by the new felt with respect to key travel, but the White keys have a reduced “throw”, and feel…. tighter. This must be because their resting position is slightly closer from where it used to be, due to the new felt strip. I expect the new felt will compress a little further as time goes by, but the difference isn’t bad. It feels like an improvement. So, yay.
I hope you’ve enjoyed this tale from the workshop, and maybe even found some information that helps you out in your projects. Drop me a line if you have questions.
Recent Comments